Improving Food Safety Compliance Is Simpler Than You Think
.jpg)
Food safety practices have made incredible strides over the last few decades. However, recent incidents serve as an important reminder that there is plenty of room to improve.
Today, I want to touch on a part of the food safety lifecycle that is simple to address but still not widely adopted by food retailers: ensuring coolers and freezers storing food are always running at the right temperature. To be clear, almost every food retailer today has a temperature monitoring strategy. It’s the execution of that strategy that I want to focus on here.
The most common temperature logging strategy in 2024 is still manual: employees walk around and manually log the temperature of each cooler and freezer by hand. They may do this every two to four hours, once at opening and again at closing, or even just once a day.
These sporadic checks leave significant gaps, where no one knows the real-time temperature of their refrigeration systems or has a complete history when issues inevitably arise. With that in mind, take a glance at the thermometer the next time you grab a to-go sandwich or yogurt in an airport or on the road.
Manual Temperature Checks Create "Risk Windows"
Let’s break down why manual checks might be passable but leave gaps that I’ll call "risk windows."
- Human Error: Manual checks rely on employees remembering and being motivated to take readings consistently and at specific times. Temperature checks may be neglected if the store is busy or understaffed.
- Labor-Intensive: Regular manual temperature checks can be time-consuming. Employees must walk from one piece of equipment to another, making it impossible to maintain real-time logs.
- Delayed Data: Since manual checks occur only a few times daily, staff may miss equipment failures or temperature spikes for hours. These gaps leave everyone at risk.
So, if the risks are so blatant and windows of risk so frequent, why is automated temperature monitoring not more common? Until recently, no solutions could operate reliably in harsh environments like quick service restaurants (QSRs) and convenience store walk-in freezers over long periods.
The Benefits of Automated Temperature Monitoring
That’s where Disruptive Technologies comes in, with wireless sensors that make temperature monitoring simple.
%2520(5).png)
With a solution like this in mind, let’s compare the benefits of automated temperature monitoring compared to manual monitoring:
- Staff Can Focus on Customers: Tiny sensors track temperature data 24/7 with no maintenance or labor, regardless of how busy the store is.
- Real-Time Alerts: Automated alerts are sent to the right place at the right time, alerting store personnel or a centralized help desk of the issue.
- Full Compliance: No more guesswork or gaps where there are no temperature logs. Fully traceable data is at your fingertips.
Conclusion
While manual temperature checks may seem sufficient for ensuring food safety and compliance with regulations, the potential for human error, resource drain, and delayed issue awareness make them far less effective than automated temperature monitoring.
By investing in sensors and automation, grocery stores, convenience stores, and restaurants can ensure consistent, accurate, and reliable temperature monitoring, ultimately protecting their customers, products, reputation, and bottom line.
In today's world, automation isn't just a convenience—it's essential for maintaining the highest standards of food safety and operational efficiency.
Join the Movement
This simplicity of the Disruptive Technologies solution ensures that organizations like RaceTrac and H&S Energy can efficiently manage their assets, prevent breakdowns, and protect their customers and products.
Discover how RaceTrac Doubled Down on Food Safety with Next-Generation Temperature Monitoring
If you currently rely on manual temperature monitoring and logging, you too could benefit from reliable data from sensors that are affordable, easy to set up and easy to scale, and last as long as the equipment itself.
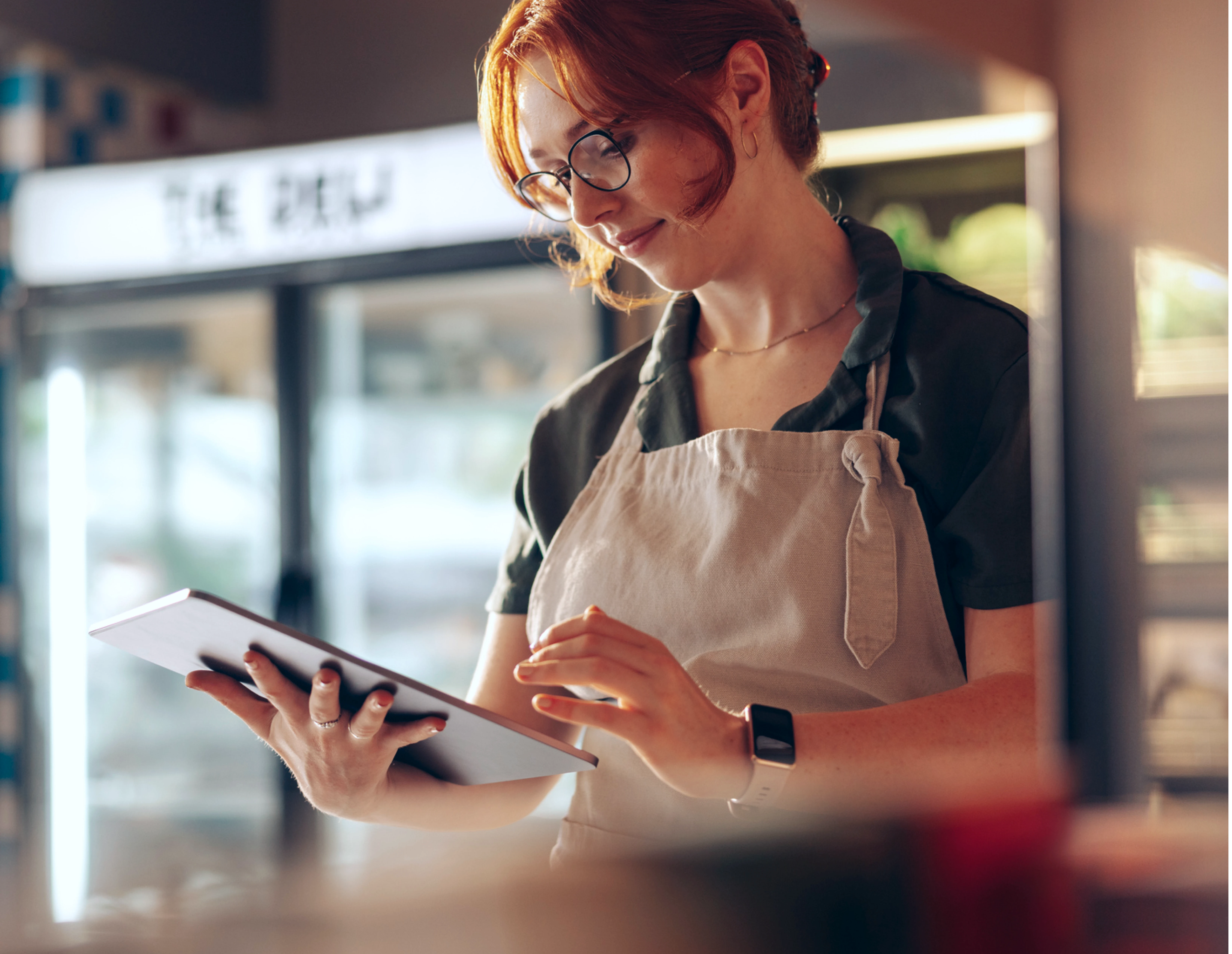
Discover our Cold Storage Monitoring Solution
Get Started
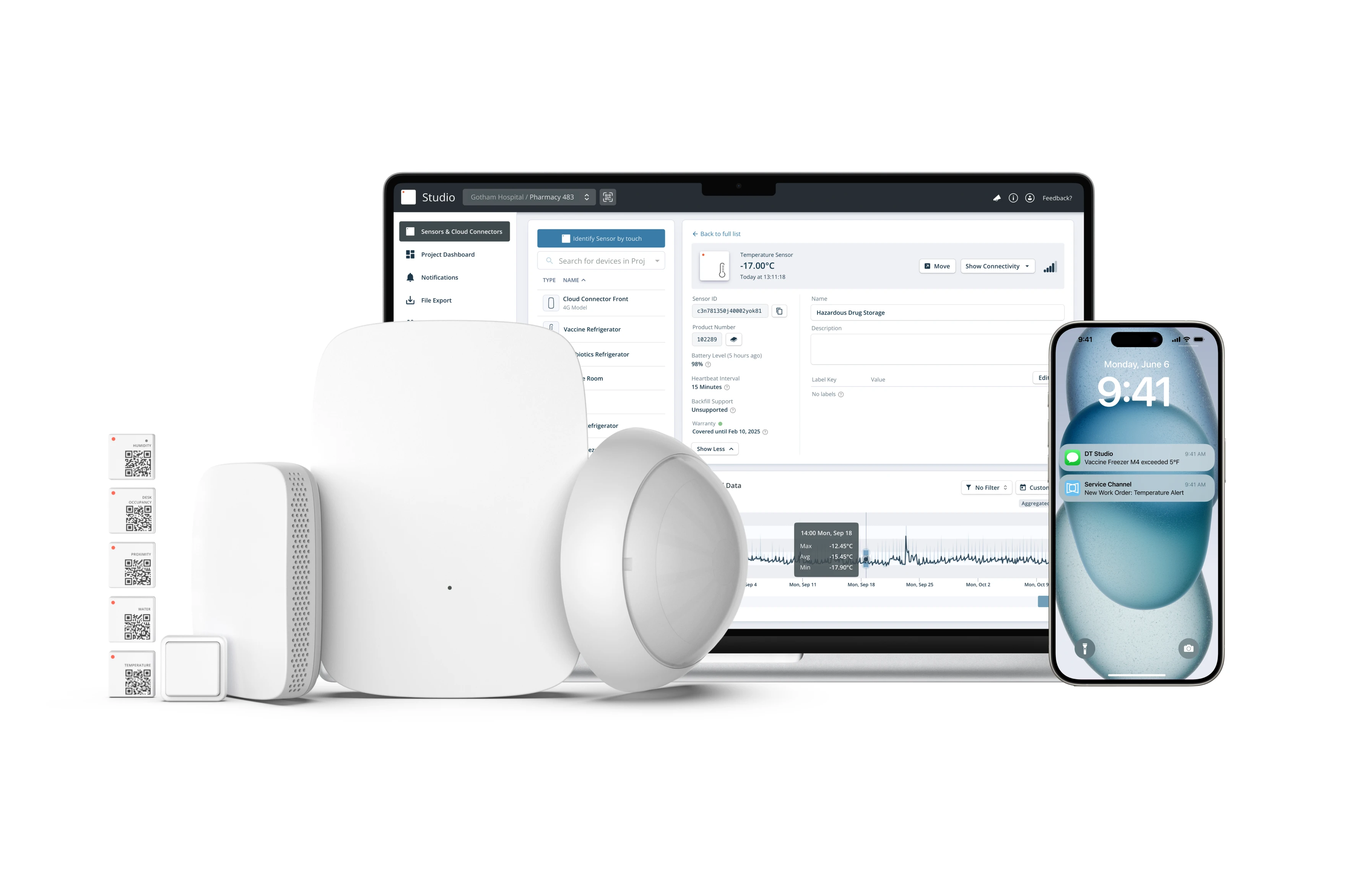