RaceTrac Doubles Down on Food Safety with Next-Generation Temperature Monitoring
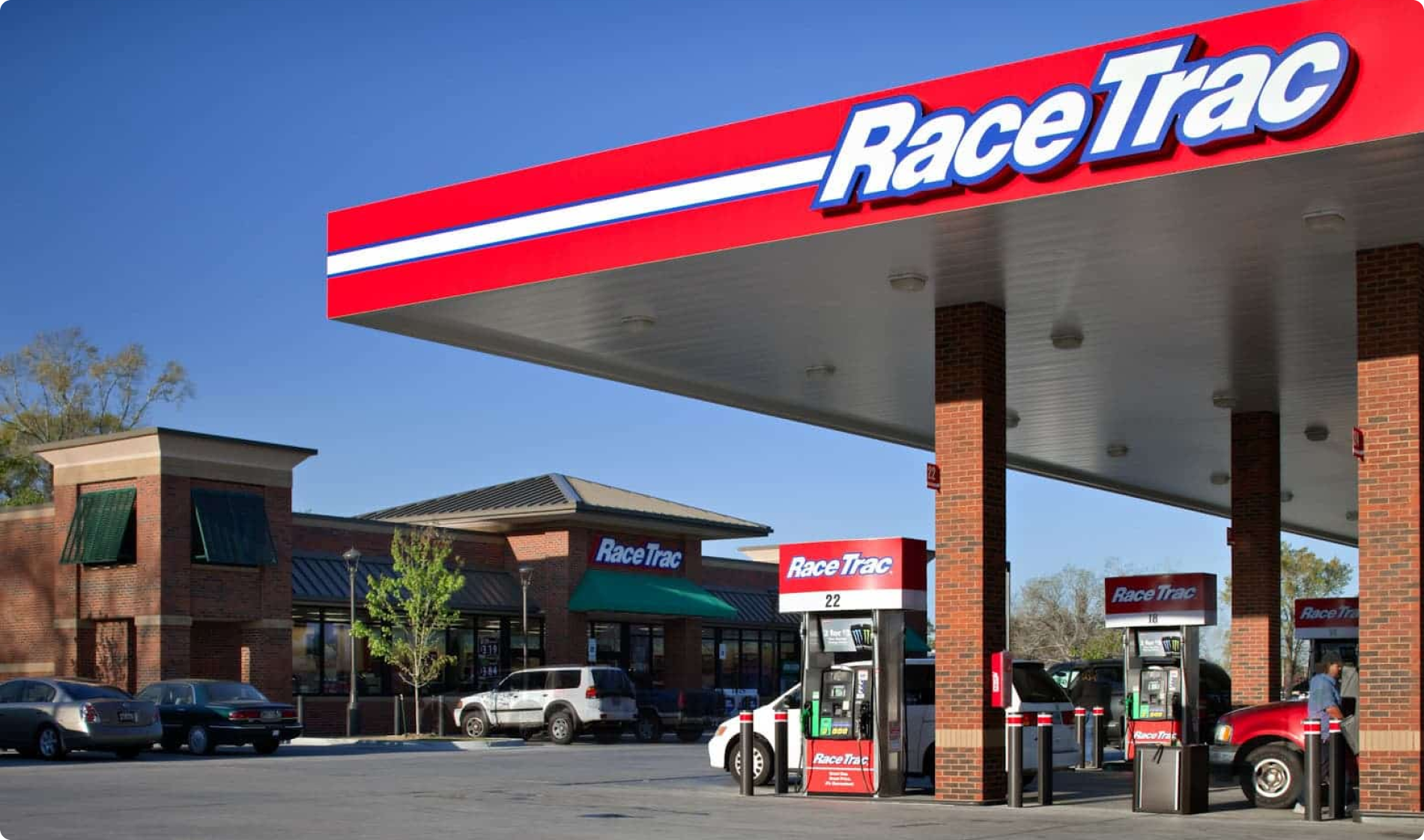
RaceTrac, a leading convenience store chain in the U.S., has successfully deployed the Disruptive Technologies automated temperature monitoring solution across its 580 locations. This landmark project underscores RaceTrac’s ongoing commitment to providing its guests with safe and fresh food while significantly increasing operational efficiency. At the same time, the partnership solidifies Disruptive Technologies’ position as the definitive leader in large-scale, remote temperature monitoring rollouts.
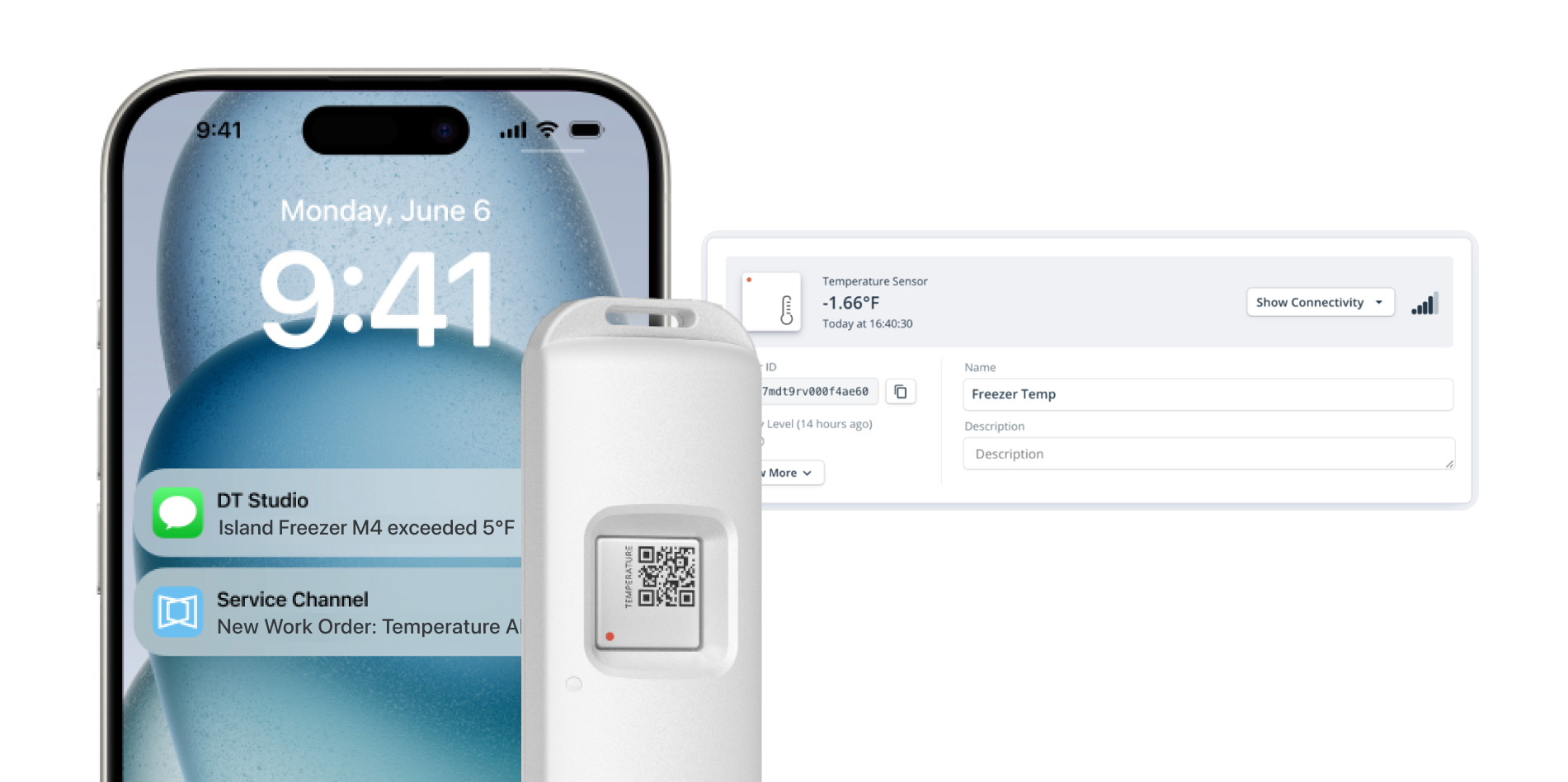
A Solution That is “Simply Better”
The team at RaceTrac was initially intrigued by the family of tiny wireless sensors that can monitor everything from temperature to CO2. "We ultimately chose Disruptive Technologies for its reliability and 15-year battery life,” says Chase Roth, Special Projects Manager at RaceTrac. “When we tried other temperature monitoring systems, we experienced higher-than-expected sensor failure rates and lower-than-anticipated battery life, increasing the cost of maintaining the system. The performance of the Disruptive Technologies sensors was simply better.”
470 Stores in Under 7 Weeks
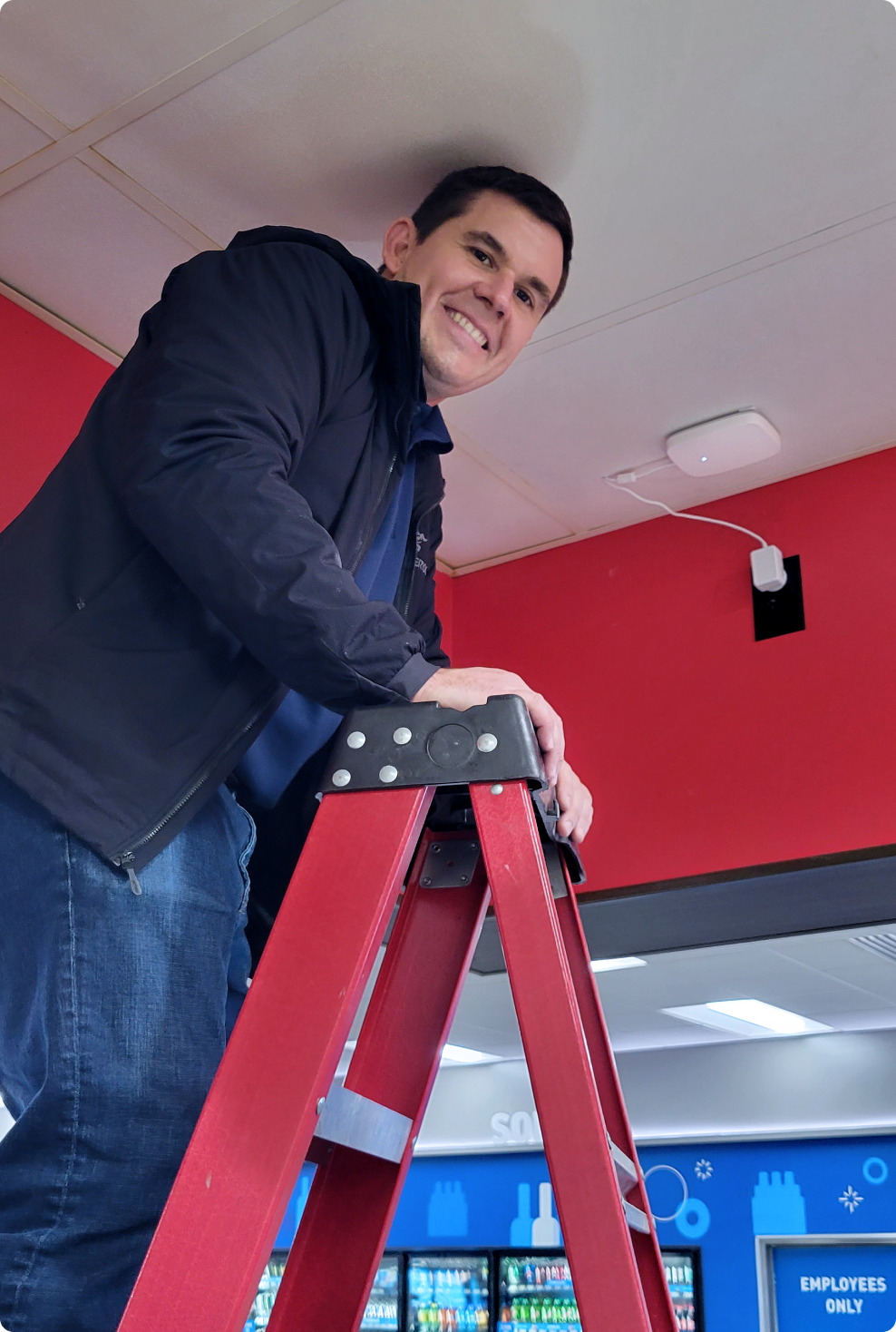
Making the transition simple and easy for RaceTrac was critical to the project's success. Following the first wave of pilot installations, the Disruptive Technologies Professional Services Team equipped the final 470 stores with temperature sensors in under 7 weeks.
“We experienced almost no issues during the rollout across 580 stores. To have so few problems over a fleetwide rollout is unique in our world,” says Chase Roth.
Equally important was rapidly completing an integration with ServiceChannel, RaceTrac’s work order management system. With the integration, temperature alerts from sensors in refrigerators, freezers, and hot cases alert RaceTrac’s Help Desk to equipment requiring attention.
Walter Sears, Head of Operations at Disruptive Technologies, says, "The way we look at it, we are not providing RaceTrac with temperature monitoring sensors; we are supplying them with helpful work orders."
One Alert Can Save $800 Worth of Fresh Food Products
If a critical rise in temperature in a cooling unit is identified too late, the food held must be removed from the unit and thrown away. With automated temperature monitoring, RaceTrac can identify an issue before the food is compromised and take action before they have to throw anything away.
Chase gives an example, "We can pull fresh food items from a cooler that isn't working properly off the sales floor into another cooler and save all that food from being wasted. When the cooler is working again, we can put the food back out for sale and save seven or eight hundred dollars worth of product".
Josh Tate, RaceTrac's Director of Store Operations, explains it like this: "Before, when we checked things manually, we might only catch that a product's temperature was too high at 1 pm. But it could have been too high since 11:30 am, which would still be safe to sell. However, if it had gone bad at 8 am, we'd have to throw it out because it was outside the four-hour safety window. With the Disruptive Technologies system, we know exactly when a problem happened and can fix it before we waste anything."
Ensuring Helpful Work Orders
The support team running the RaceTrac Help Desk experiences a difference in the reliability of the alerts created by Disruptive Technologies sensors. "With other systems, we experienced a lot of noise tickets that the Help Desk had to handle, even though there wasn't an actual issue with our equipment," says Josh. "They would call the store and find out it was a false alarm. If that happens regularly, a lot of time is wasted. The Disruptive Technologies team was great at identifying ways to ensure that didn't happen, so the Help Desk has a lighter load."
The Future
With the automated temperature monitoring solution fully installed and the effort of maintaining the system dramatically reduced, Josh Tate, Director of Store Operations, talks about the future: "We’re looking into different ways to use the data Disruptive Technologies provides to bring efficiency and insight to our operations. That could be predictive maintenance, identifying equipment anomalies, monitoring doors and windows, or adding humidity data. The more data we have, the smarter we can be."
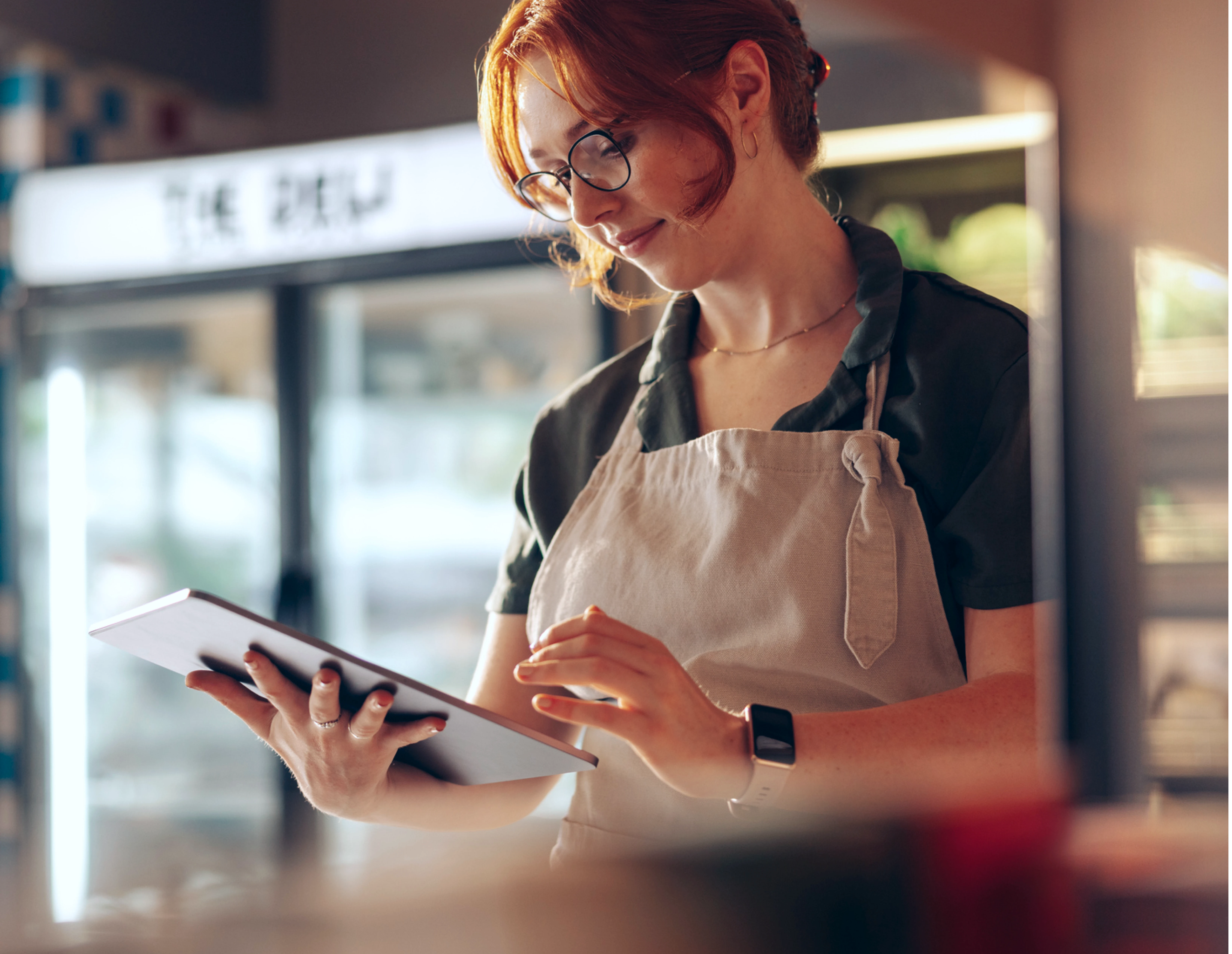
Discover our Cold Storage Monitoring Solution
Get Started
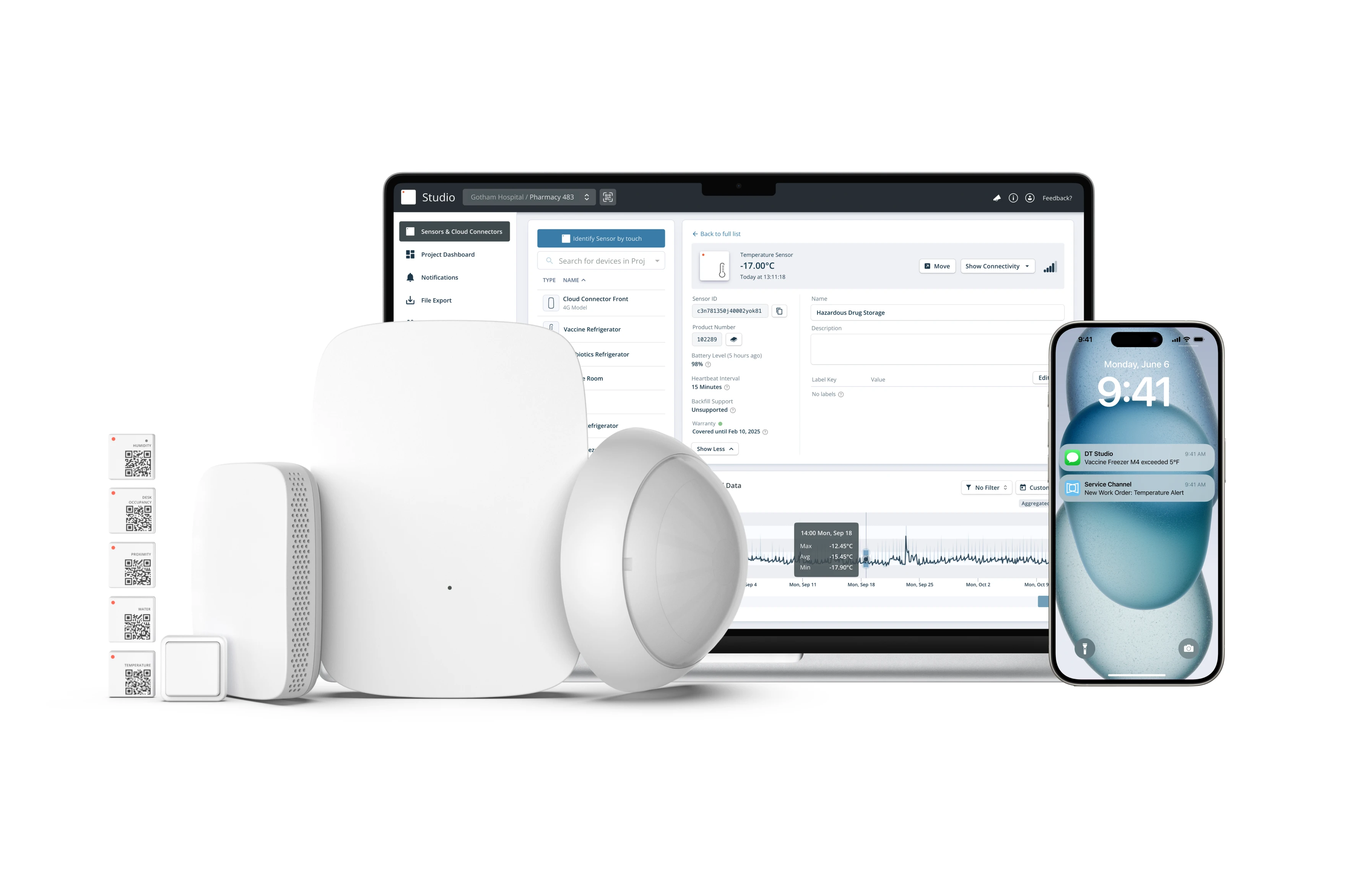