Sensor-Based Predictive Maintenance of Equipment Installed In Explosive Atmospheres [Ex Certified]
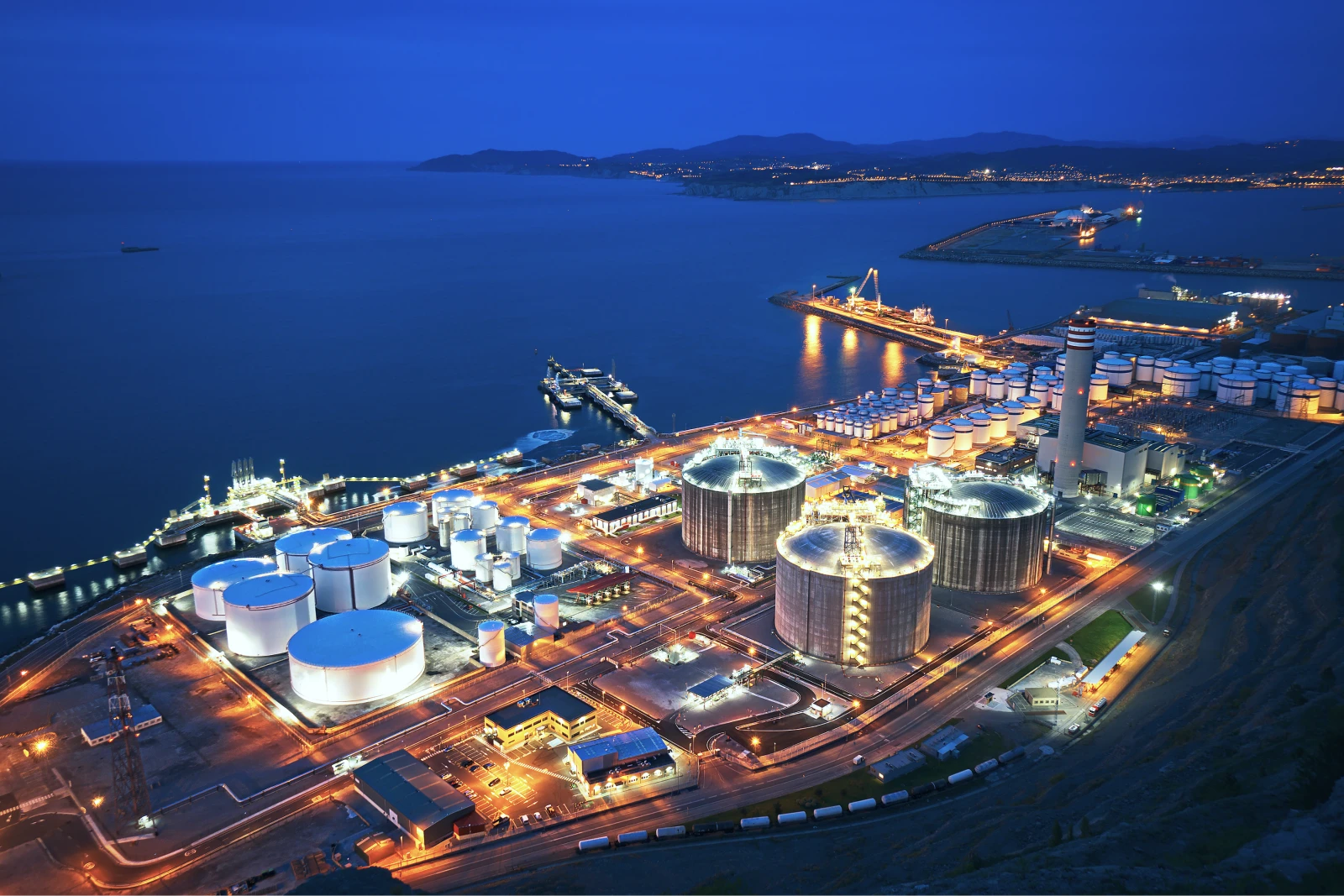
Electrical equipment maintenance accounts for some of the highest operating costs in explosive atmospheres. Much of a company’s time and resources in the Hydrogen, PetroChemical, Pharmaceutical, and Oil and Gas industries are spent on inspecting and maintaining critical equipment.
Most inspections and maintenance of equipment within (or just in) explosive atmospheres are conducted so that equipment follows regulatory requirements for potential ignition sources. To date, these inspections and subsequent maintenance are based on static, calendar-based systems and maintenance programs.
We have recently partnered with Ex-tech Group, a fellow Norwegian company and an innovator for explosion protection and compliance to digitize explosive atmospheres through our wireless sensing system. Now refineries, process plants, offshore structures & more companies with explosive atmospheres can enjoy a reduction in manual inspection and error, increased efficiency, and safer areas.
What Is An Explosive Atmosphere?
An explosive atmosphere is an area in which the air contains or may contain a sufficient quantity of flammable or explosive material, gases, dust, or vapors.
Examples of explosive atmospheres include:
- Refineries and processing plants
- Offshore structures & platforms
- Ships/vessels in oil & gas, both carriers and production facilities
- Terminals and pipelines
- Storage facilities
Explosive atmospheres are prone to fires or explosions when 3 basic conditions are met: oxygen, fuel, and an ignition source. To protect areas from a potential explosion, equipment that contains ignition sources needs to be built as “Ex equipment”. Ex equipment are assets that comply with regulations for hazardous installations.
Whenever an area is defined as a potentially explosive atmosphere, facilities need to be monitored and protected from potential ignition sources. This is done in accordance with the protection principles described in Atex directive 2014/34/EU in the European Union (FUSEX in Norway).
Since the monitoring process has been manual to date, which takes up time and can produce errors, managers of explosive atmospheres need to find more intelligent ways to conduct their maintenance.
Classification of Explosive Atmospheres
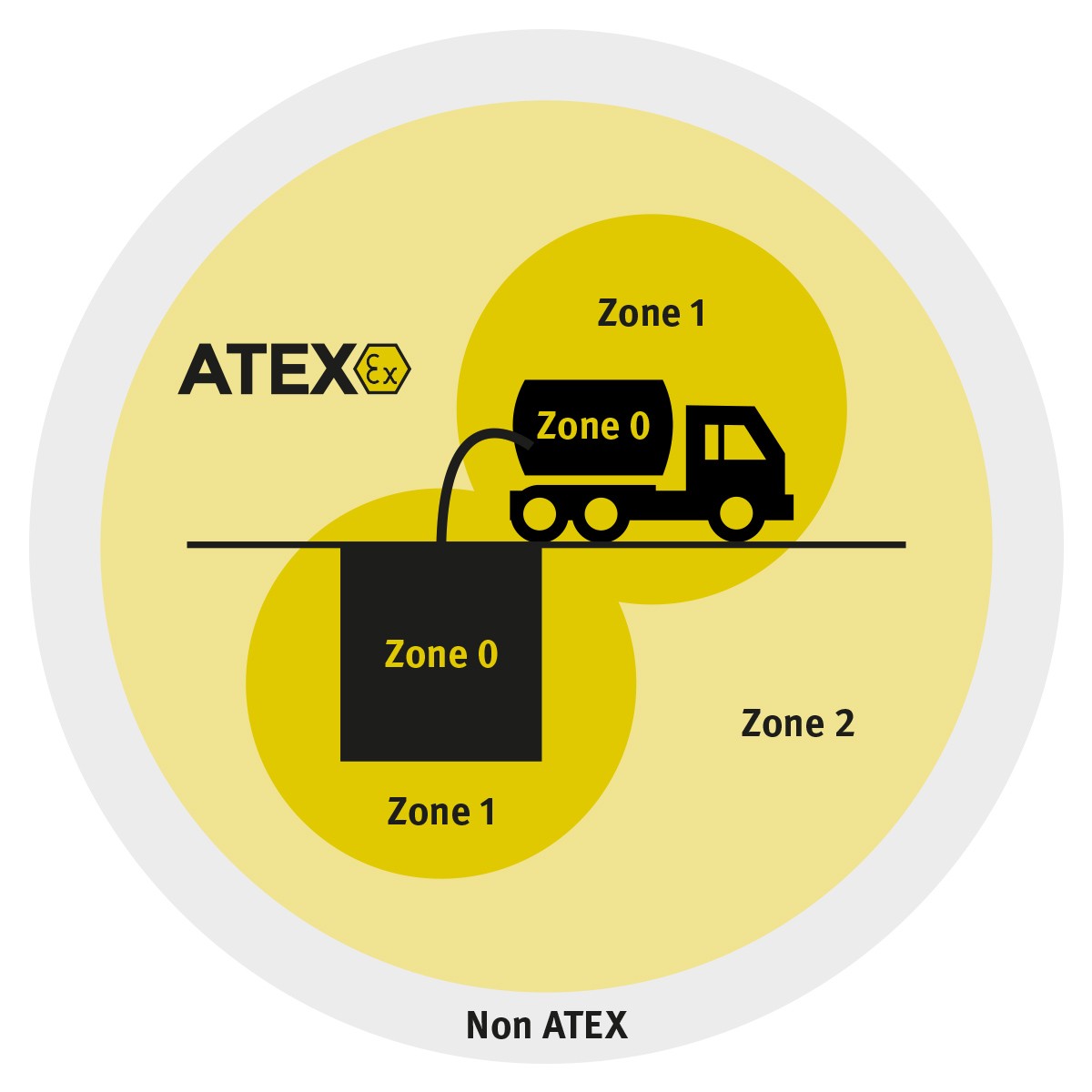
Explosive atmospheres can be classified into three categories (Zones) depending on the volume of an explosive atmosphere in the air:
- In a Zone 0 explosive atmosphere, there is an explosive atmosphere for more than 1000 hours per year.
- In a Zone 1 explosive atmosphere, there is an explosive atmosphere between 10 and 1000 hours per year.
- In a Zone 2 explosive atmosphere, there is an explosive atmosphere for less than 10 hours per year, but the contents of the air still make control over ignition sources a necessity due to the risk of explosions or fire.
Disruptive Technologies Sensor Solutions For Explosive Atmospheres [Ex Certified]
Sensors that are mainly installed in or together with other Ex protected equipment (cabinets, boxes, control stations, motors, luminaries, etc.) need their own Ex certified explosion protection.
With the exception of conditions that can be visually detected by maintenance staff during manual inspections, there are currently no wireless systems that can detect changes at an early stage. An undetected interruption, therefore, can escalate or lead to costly downtime and even critical operational situations. There is an increasing need for a robust, reliable, Ex certified wireless sensing system in explosive atmospheres that can take the guesswork and errors out of maintenance. We can now answer to that need.
Disruptive Technologies sensors are the smallest in the world (19 x 19 x 2.5 mm), have an IP68 rating, and can withstand very high temperatures. They are now officially certified by the Ex-tech Group, the Norwegian explosion protection and Ex compliance expert, to be placed in explosive zones.
The sensors can measure critical parameters in explosive atmospheres, like humidity, water, temperature, and proximity. They can be installed directly on/in other Ex protected equipment since they have their own Ex protection.
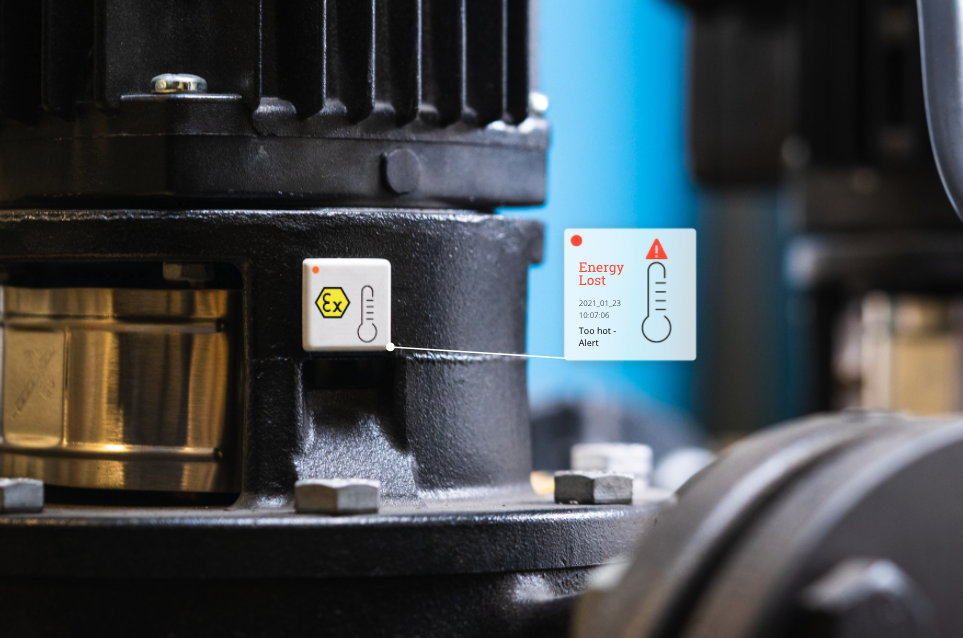
Download Sensor Ex Certification.
The sensor solution offers continuous accurate monitoring and reporting of operational data. Through alerts and automation, staff receives warnings of faults and incidents before they happen, guaranteeing fewer incidents, increased equipment lifetime, and peace of mind. Managers and workers optimize time and manual work on inspection and maintenance of critical equipment to spend time on more creative and rewarding work.
Hydrogen, Oil & Gas, Petrochemical, and Pharmacy companies can now remotely operate, monitor, and control their installations onshore and offshore at a fraction of the cost, reducing manual work, preventing incidents, and gaining accurate important insights that benefit profit, people, and the planet.
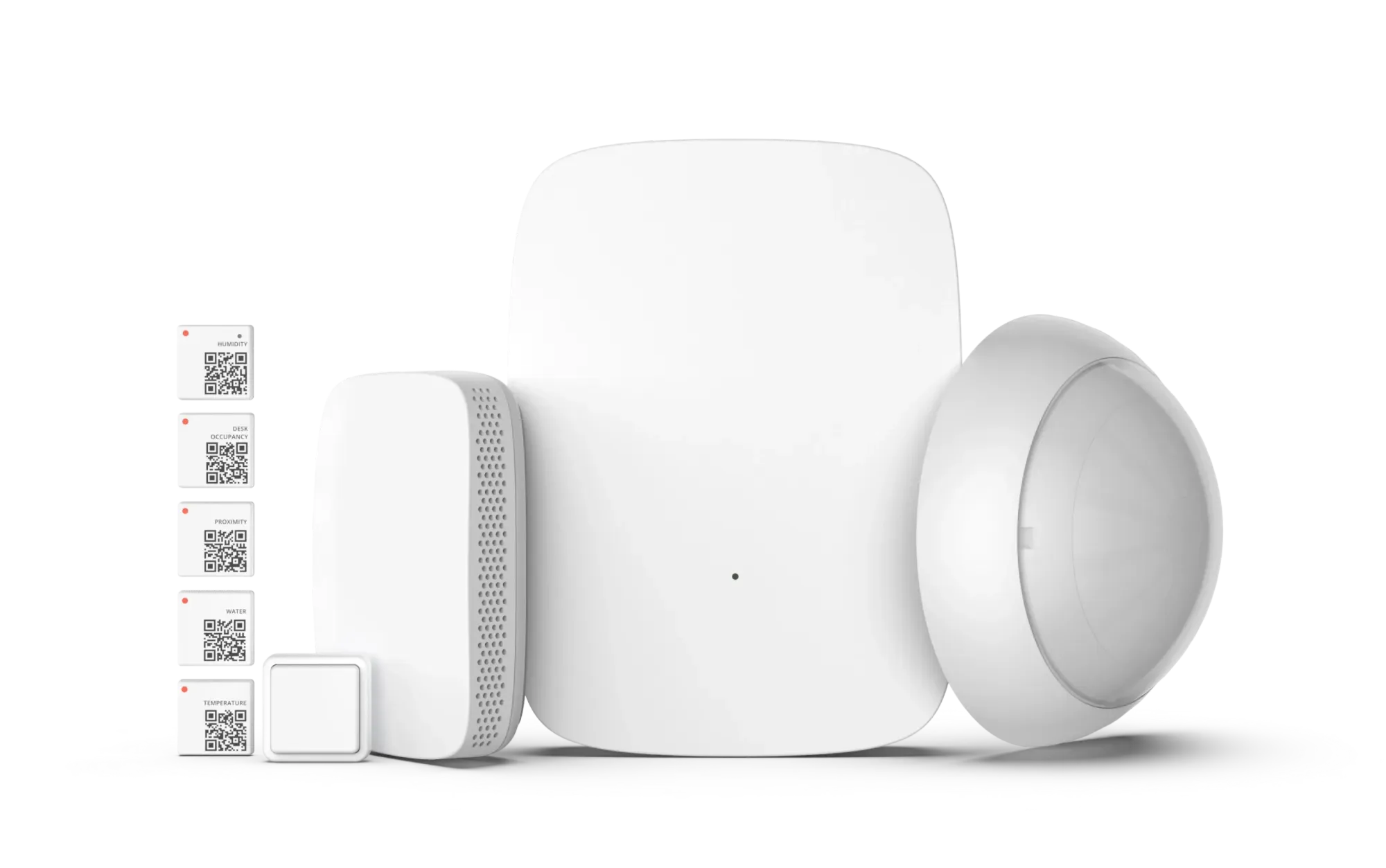
Easy-to-Deploy IoT Sensors & Infrastructure
Content That Might Interest You
Get Started
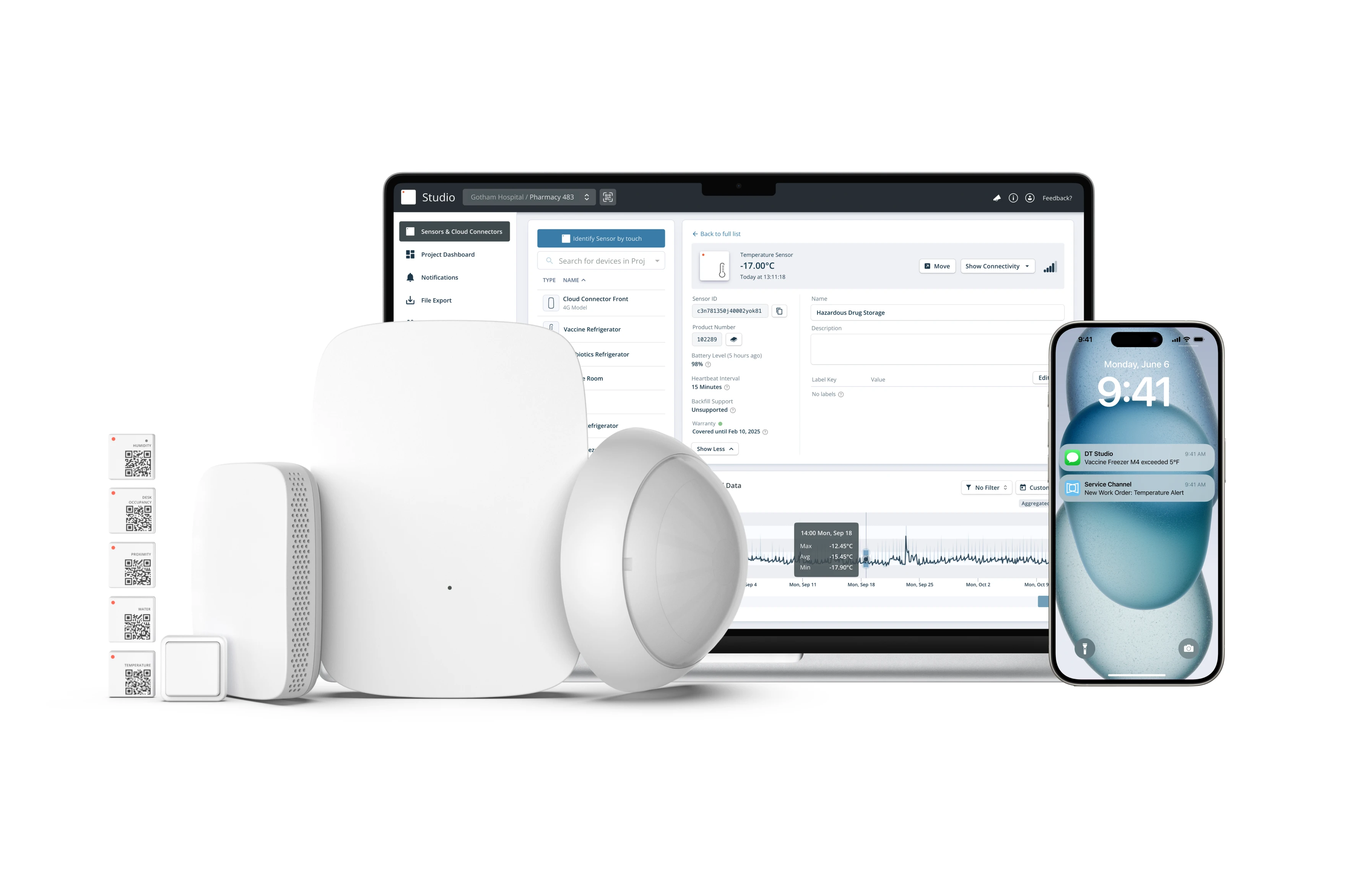