The Future of Temperature Monitoring: Say Goodbye to Manual Checks
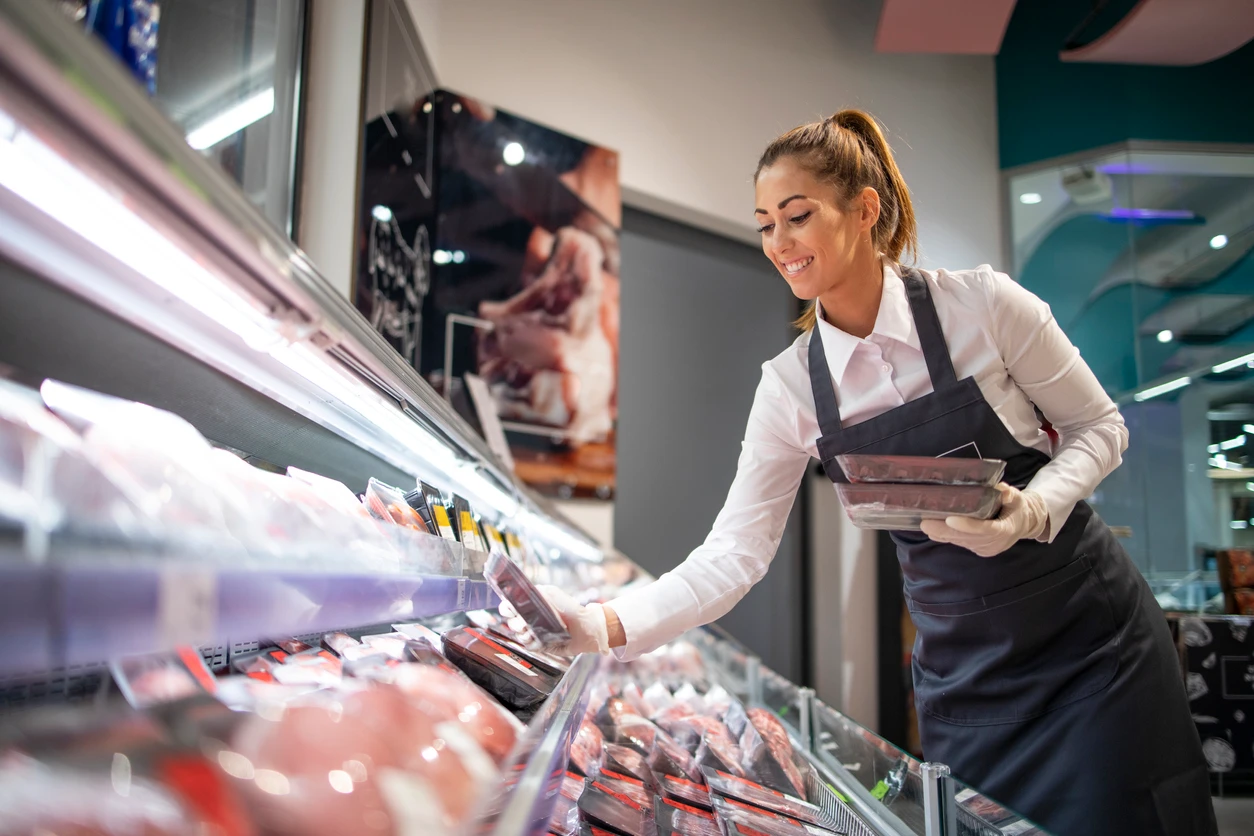
Technology is making food spoilage a thing of the past, protecting retailers from profit loss, ensuring food is safe and compliant, and bringing peace of mind to operations teams responsible for ensuring that fresh products are kept at the right temperature to ensure quality and safety.
The traditional method of manually monitoring refrigeration units is inefficient and inaccurate. Factoring in the ongoing labor shortage, it is also becoming increasingly unsustainable. In this article, we explore the limitations of manual temperature monitoring and the new temperature monitoring system that promises to improve cold storage management dramatically.
The Problem with Manual Temperature Monitoring
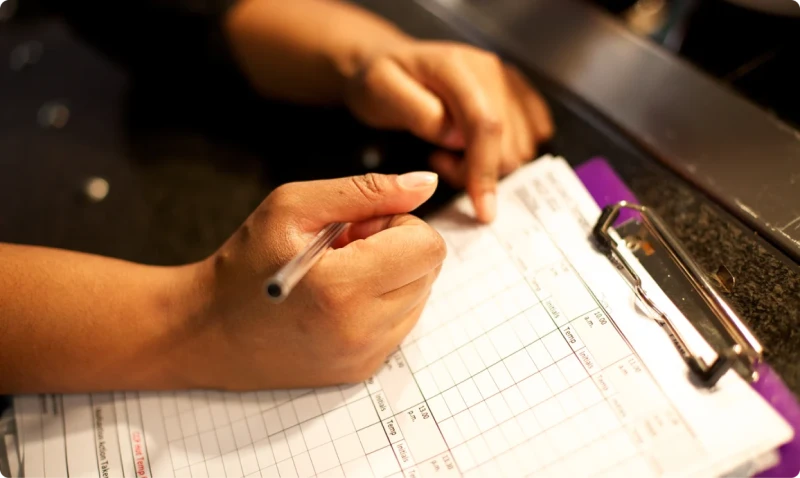
Cold storage equipment needs to be kept at an optimal temperature to extend the shelf life of food products and ensure food safety compliance. However, relying on manual temperature checks comes with several challenges.
First, human error can lead to inaccurate readings, jeopardizing the quality and safety of stored goods. Routine manual tasks are sometimes skipped or not performed carefully enough, impeding the timely identification of temperature fluctuations that can lead to food waste or compromised integrity.
Another issue with manual checks is that incidents can be missed. For example, if a power outage occurred when the facility was closed and lasted for many hours, the temperature of refrigeration units could be back at desired levels by the time the next scheduled check took place. Staff wouldn’t know that the quality and safety of the food stored inside had been compromised.
Operational Efficiency in the Face of Labor Shortages
The retail industry faces a labor shortage crisis that is worsening rather than improving. Food retailers must use personnel in the most efficient way possible. Manual equipment monitoring demands human resources, diverting valuable labor from other critical tasks.
The industry must explore alternative methods to streamline operations and reduce reliance on manual intervention to keep staff focused on activities that drive customer satisfaction. The strain on resources can also mean that checking the temperature of storage equipment isn’t prioritized, increasing the risk of a failure going undetected.
Advancements in Sensor Technology
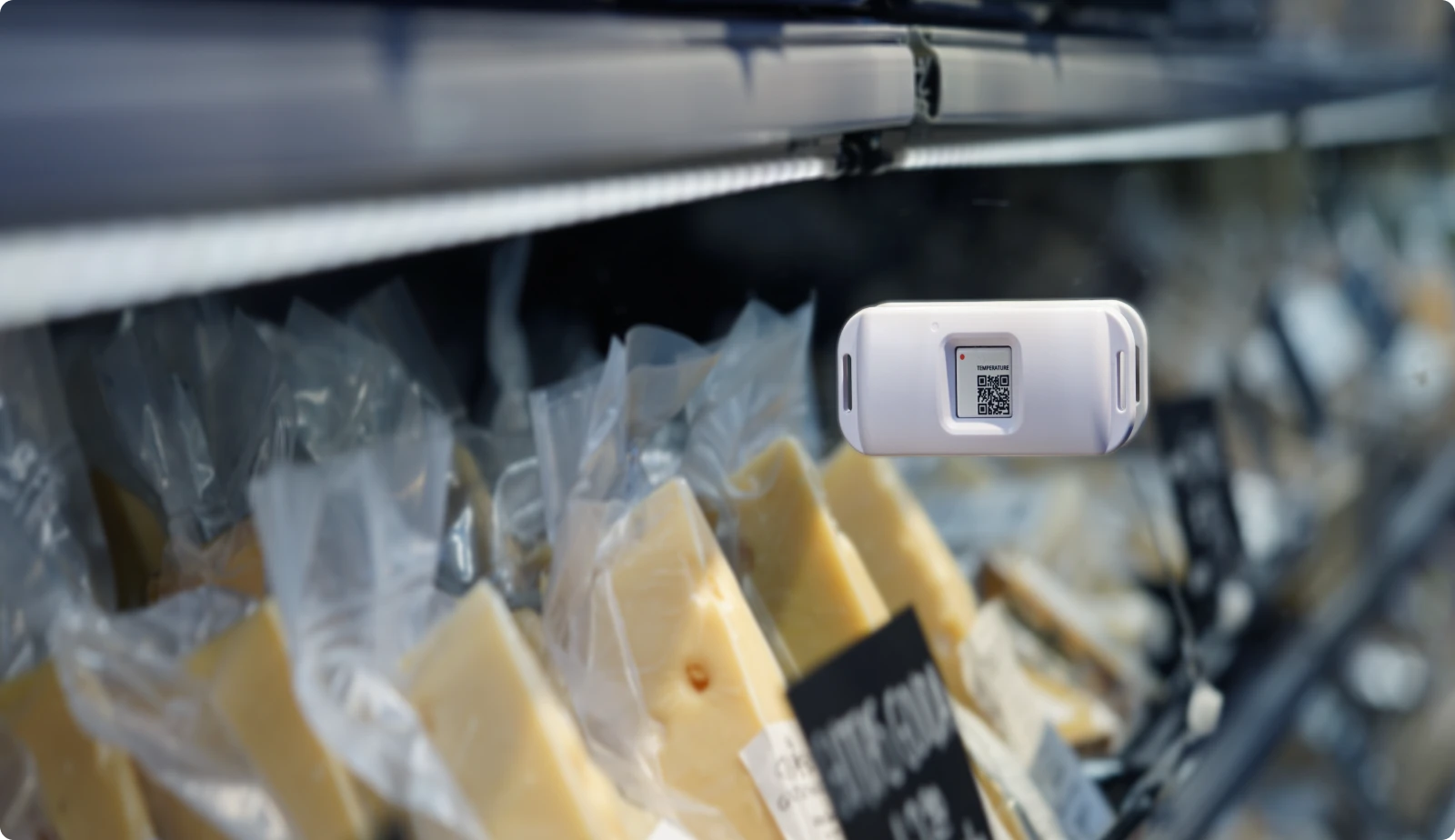
Despite the problem with manual monitoring, until now, sensor technology has not been ideal for cold storage environments with limited space and extremely low temperatures. While wired solutions work well, they can be costly, and their implementation into existing infrastructure is tricky. On the other hand, some wireless sensors struggle to meet the accuracy, connectivity, and robustness requirements of cold storage.
At Disruptive Technologies, we have taken on the challenge of optimizing our sensors specifically for use in these challenging conditions. Our wireless temperature sensors are tiny and wireless. The discreet design means they can be strategically placed in fridges, freezers, and display cases to monitor temperature conditions in real-time without impacting the product display. Because cold conditions can be a challenge for battery life, we have enhanced our sensors to offer up to 15 years of battery life at temperatures as low as -40 degrees °C / °F.
The Best Solution for Cold Storage Monitoring
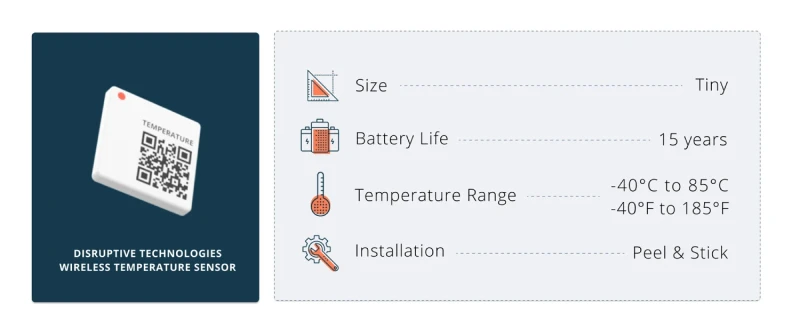
It is easy to get started. Implementation requires no investment into additional infrastructure. We provide sensors, cloud connectors, and data management software as a complete solution. If there is a need for more advanced functionality, such as automatic cooling system control, we work with partners to create solutions that further automate cold storage management.
Maintenance and Preventive Action
With the right sensor technology, cold storage facilities can proactively address potential issues before they result in food spoilage. The sensors detect variations in temperature patterns and performance. The data can then be used to trigger automatic work orders for intervention. By identifying maintenance requirements in advance, costly breakdowns and subsequent downtime can be avoided, ensuring continuous operation and food safety compliance.
The Future of Cold Storage: Remote Temperature Monitoring
The cold storage industry is at a pivotal juncture where real-time, remote temperature monitoring is finally a viable and easy-to-implement option. As labor shortages persist, embracing wireless sensor technology will be the game changer for efficiently maintaining the quality and safety of perishable goods.
Manual temperature monitoring will become a thing of the past. With our wireless temperature monitoring solution optimized specifically for cold environments, Disruptive Technologies is leading the way in helping cold storage facilities around the globe safeguard their operations, reduce costs, and contribute to a more sustainable future.
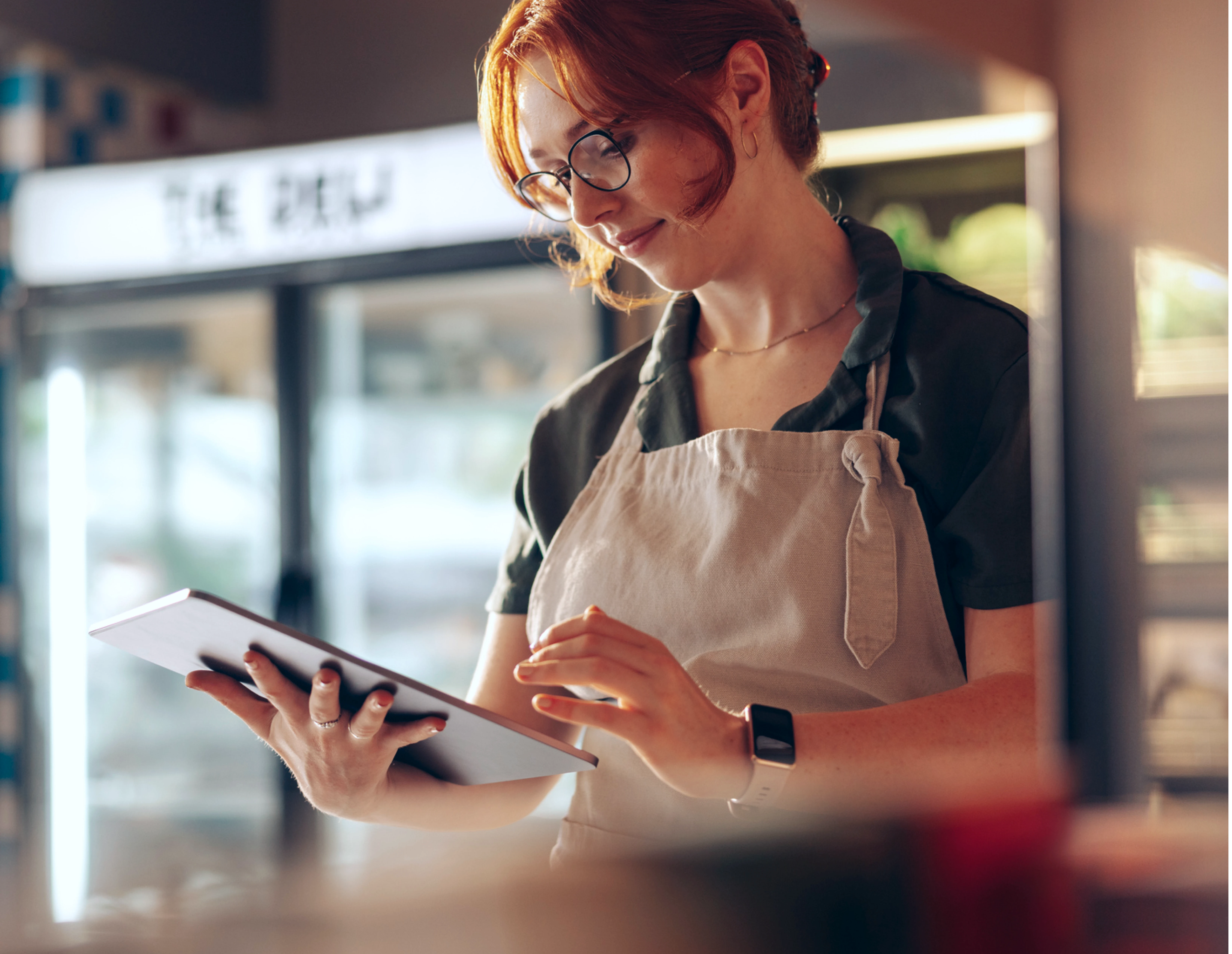
Temperature Monitoring Made Simple
Get Started
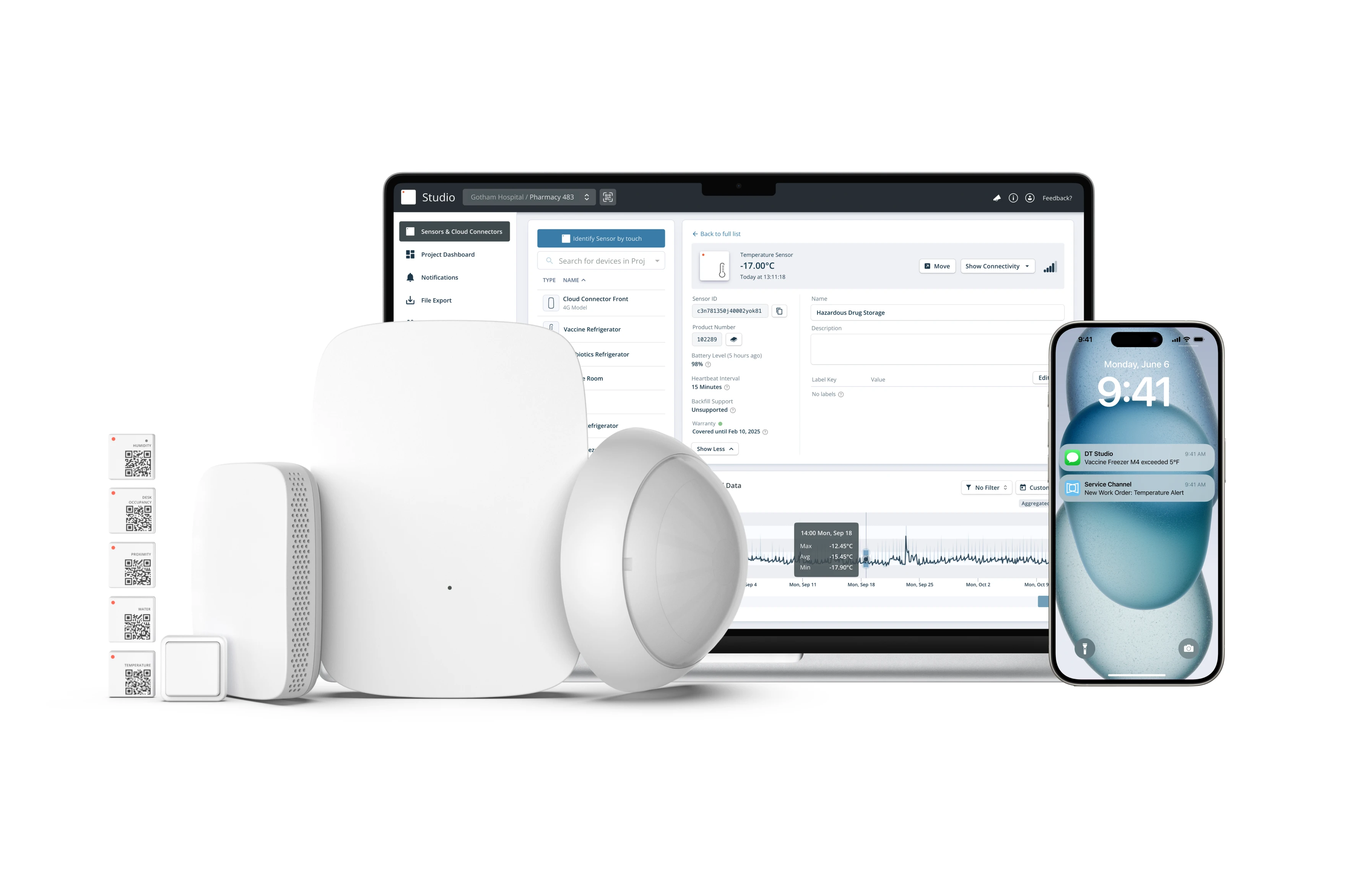